Aluminum Casting Proficiency: Strategies and Tools for Extraordinary Outcomes
Understanding the art of light weight aluminum casting needs a fragile equilibrium of accuracy, technique, and the usage of specialized tools. From the preliminary stages of thawing the light weight aluminum to the intricate process of mold and mildew preparation and putting, each step plays an important role in achieving exceptional results. As we explore the elaborate methods and devices involved in aluminum casting mastery, one can not forget the relevance of sophisticated pouring and cooling down techniques that can raise the last result. Keep tuned to reveal the vital tools and ending up touches that lead the way for impressive aluminum spreadings.
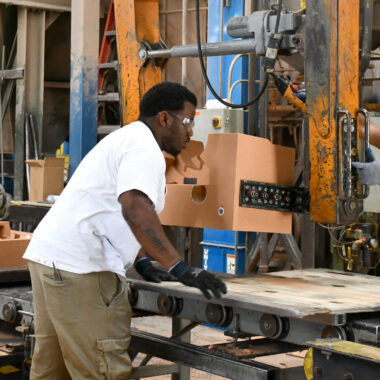
Relevance of Proper Melting Strategies
Making use of exact temperature control during the melting process is vital in guaranteeing the high quality and stability of light weight aluminum spreadings. The melting of light weight aluminum is a critical step in the casting process, as it directly impacts the final properties of the casted components. Proper melting techniques are vital to attain the desired metallurgical structure, mechanical buildings, and surface area finish of the aluminum parts.
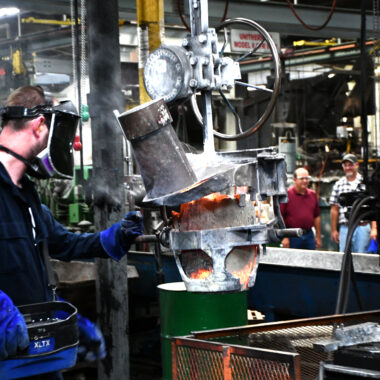
In addition, tracking and readjusting the melt temperature during the process aid stop overheating, which can trigger grain development and influence the general top quality of the light weight aluminum spreading. Abiding by exact melting strategies not only improves the high quality of the last item but likewise enhances the performance and cost-effectiveness of the casting process.
Crucial Mold Preparation Tips
Appropriate preparation of molds is a fundamental facet in the light weight aluminum casting process, ensuring the successful duplication of complex information and measurements in the last casted parts. Prior to pouring the molten aluminum, the mold tooth cavity have to be thoroughly cleaned and dried out to stop issues in the spreading.
Moreover, appropriate gating and risering style are necessary in mold prep work to ensure audio castings with marginal flaws like porosity and contraction. Eviction system promotes the flow of molten metal into the mold tooth cavity, while risers help protect against contraction by providing added liquified metal as the casting solidifies. Careful consideration of these aspects throughout mold and mildew preparation substantially contributes to the quality and integrity of the last light weight aluminum cast parts.
Advanced Pouring and Cooling Techniques
Implementing innovative putting and cooling methods is essential in enhancing the light weight aluminum casting process for boosted efficiency and quality end results. Making use of strategies such as vacuum spreading can substantially minimize porosity in the end product, bring about improved mechanical homes. By evacuating the air from the mold tooth cavity before putting, the risk of gas entrapment is minimized, resulting in a denser and even more structurally sound casting.
In addition, using regulated air conditioning methods, such as water quenching or air cooling, can influence the product's microstructure and mechanical attributes (about aluminum casting). Quick air conditioning can help achieve better grain frameworks and improved mechanical buildings, visit here making the actors light weight aluminum better for applications needing high strength and durability
In addition, applying directional solidification techniques, where the spreading solidifies gradually from one end to an additional, can assist alleviate interior defects and improve total component stability. By meticulously taking care of the temperature differentials during solidification, the formation of shrinking porosity and hot splits can be lessened, leading to better spreadings with enhanced mechanical performance.
Important Tools for Aluminum Casting
Enhancing the efficiency and top quality end results of aluminum casting procedures counts greatly on the use of specific tools designed to maximize different facets of the casting operation. One vital tool for light weight aluminum spreading is the crucible. Crucibles are containers made of materials like clay-graphite or silicon carbide that endure the heats required for melting aluminum. Crucibles can be found in numerous sizes to accommodate various spreading quantities and are vital for melting and putting the liquified aluminum.
An additional vital device is the mold and mildew. Mold and mildews can be made from materials like sand, plaster, or steel and are used to shape the liquified light weight aluminum into the desired kind. about aluminum casting. Appropriate mold layout and products are essential for accomplishing exact casting measurements and surface coatings
In addition to crucibles and mold and mildews, a furnace is an essential tool for light weight aluminum spreading. Heaters heat up the metal to its melting factor, guaranteeing it remains in a state ready for casting. Crucial for preserving constant temperatures and guaranteeing the aluminum stays liquified, heaters are readily available in numerous kinds, such as electric, gas, or induction furnaces, each with its benefits for certain casting demands.
Ending Up Touches and Quality Checks
Upon completing the casting procedure, thorough focus to ending up touches and strenuous high continue reading this quality checks is extremely important to make certain the integrity and accuracy of the light weight aluminum elements - about aluminum casting. Completing touches entail the removal of any kind of excess product, such as flash, gating systems, or harsh edges, to achieve the preferred final shape and surface area quality. This step typically consists of processes like grinding, fining sand, or shot blasting to improve the look and texture of the cast parts
Quality checks are after that carried out to verify that the parts fulfill the specific needs and criteria. These checks might include dimensional assessments making use of precision devices like calipers or coordinate gauging machines to make sure precision. Furthermore, non-destructive testing methods such as ultrasonic testing or X-ray evaluation can be utilized to identify any kind of interior defects that may compromise the structural stability of the parts.
Conclusion
In verdict, mastering aluminum casting methods and utilizing the right tools is vital for attaining remarkable results. Appropriate melting techniques, mold prep work, pouring and cooling down techniques, as well as completing touches and high quality checks are critical action in the spreading process. By adhering to these steps meticulously and making use of the proper tools, one can make sure a top quality and effective light weight aluminum spreading manufacturing.
As we check out the complex strategies and devices involved in light weight aluminum spreading proficiency, one can not neglect the relevance of innovative putting and cooling down methods that can elevate the final outcome.Proper preparation of mold and mildews is a fundamental facet in the aluminum read what he said casting process, ensuring the successful replication of intricate information and measurements in the final casted elements. Prior to pouring the liquified aluminum, the mold dental caries have to be thoroughly cleansed and dried to avoid problems in the casting.Enhancing the performance and quality outcomes of aluminum casting procedures counts heavily on the application of particular devices made to maximize numerous facets of the casting operation.In addition to mold and mildews and crucibles, a heater is an essential tool for aluminum casting.